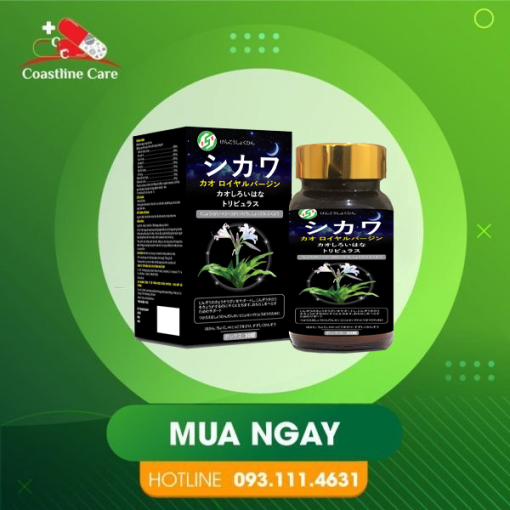
Notre guidebook complet sur la SCI a pour objectif de vous informer sur le fonctionnement et la création de votre société civile.
A fishbone diagram, often called an Ishikawa or bring about and influence diagram, supplies a visual representation of potential causes bringing about a specific problem or outcome.
P: Irrespective of whether freshly formed or taken from an Ishikawa diagram, the hypothesis should make some type of prediction (or system
Her presentation encouraged me to also become a presenter at ASQ’s various entire world conferences. With the minimal little bit of time I invested there I could inform that she’s a great teacher having a enthusiasm for sharing the fabric.
For efficient brainstorming strategies when developing an Ishikawa diagram, think about the next recommendations:
It is often made use of in additional advanced industrial environments wherever the additional types have a big effect on method outcomes.
That can help structure the tactic, the classes are often chosen from one of many frequent products demonstrated down below, but may well emerge as something special to the application in a certain case.
The Ishikawa diagram was developed while in the forties by Kaoru Ishikawa, a Japanese chemical engineer. Ishikawa, viewed as among the pioneers in high quality management, designed this Resource that will help teams Evidently visualize the different results in of a problem and how they interconnect.
Nous utilisons des cookies pour recueillir des données anonymes sur votre utilisation de notre site. Ces informations nous aident à améliorer votre expérience en ligne en comprenant mieux remark vous interagissez avec notre contenu et nos fonctionnalités.
This nha thuoc tay manual lets you find out about exactly what is the Ishikawa Diagram, the 6 M's of production as well as actions to generate your individual Diagram.
ZARK really helps to help your plant KPIs with much better monitoring capabilities on rotation machine situations with less nha thuoc tay unpredicted stops, better in-time maintenance.
Each category is analysed with regards to how it could lead to the basis dilemma. The brings about will often be damaged down further more into a lot more certain components, and when making an Ishikawa chart, team brainstorming is commonly applied.
Triggers of a part not remaining put in could be outlined as sub-branches, but the precedence must be on identifying When the section was put in or not. If a part is not effectively set up, then use the five Whys on that A part of the Ishikawa diagram for investigation.
The lights could be a contributing cause, nevertheless it nha thuoc tay really should not be the main 1 investigated. The Ishikawa diagram needs to be expanded each time five Whys is made use of. As an example, the department may well turn out as substance → portion not set up → employee skipped Procedure → get the job done natural environment way too darkish → inadequate lighting → light bulbs burned out.